MasterCAM surfacing Tutorial[edit | edit source]
Surfacing is a feature that allows you to cut a three dimensional contour on a part. It is typically done in two in two steps, a ‘Rough’ pass and a ‘Finish’ pass. Two increase the quality of the surface finish a smaller tool with tighter cuts can be used but this will increase the time it takes to machine the part.
Image |
Step
|
|
- The schools version of MasterCAM allows you to work directly with SolidWorks. From the ‘files of type’ drop down menu select SolidWorks files. Open the desired SolidWorks part file in MasterCAM.
- Once the part appears, press F9 to bring up the X, Y, and Z axes. This will help you see where the current location of the origin is on your part.
|
|
Define the origin by selecting the entire object (part).
Go to the transform toolbar --> select Translate --> select Move in the top of the Translate dialog box --> Select the +1 button
then select the new origin on the object which should be one of the top corners. Set the X, Y, and Z fields at the top of the screen in to “0”, and then press ENTER. Then press the green checkmark .
|
|
Select from the drop-down menu Machine Type > Mill flyout > and select C:\MCAMX\CNC_MACHINE\HAAS_MILL.MMD. In the Toolpaths tab in the left section of the screen, Machine Group 1 appears.
(If this doesn’t work, can do Machine Type>Mill Flyout>Manage List and select GENERIC HAAS 3X MILL.MCAM-MMD)
|
|
Expand Properties under Machine Group 1 and Select Stock Setup. The Machine Group Properties dialog box appears. In the dark-gray field, enter the dimensions of the stock piece of material that will be used. Also, using the arrow provided select the corner that will be the origin. Check the Display and Wireframe boxes on the left side of the Machine Group Properties dialog box. Select the green checkmark . The part should now be enclosed in a red-dashed box. If it is not you can change the location of the origin on the stock my moving the arrow in the dark grey field to the correct corner.
|
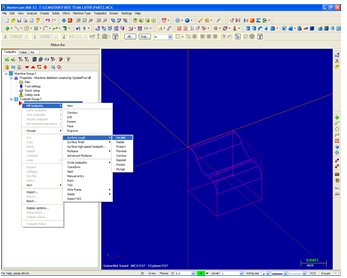 |
Right-click red arrow in the Toolpath tab > select Mill Toolpaths > Surface Rough > Parallel.
When the Select Boss/Cavity dialog box appears, select Undefined then green checkmark .
Select green check mark on Enter new NC name dialog box.
Select the desired contour on the part to be surfaced. The part will appear yellow. Press ENTER.
The Toolpath/Surface Selection dialog box appears. Select green checkmark.
|
|
- In the Surface Rough Parallel dialog box, click Select Library tool. The tool library will appear. For a surfacing feature, you will want to use a ball end mill. The size of the ball end mill depends on your part. Talk to Russ about the correct size ball end mill.
- After selecting the appropriate ball end mill, click the green checkmark . Go to the Rough Parallel Parameters tab in the Surface Rough Parallel dialog box. The Max Step over will need to be changed to accommodate the bit being used and the desired surface finish. It is a rule of thumb to set the Step over to half the diameter of the bit. The Max Stepdown will now need to be set. It is a function of the cutting speed and of the material hardness. The rule of thumb for this situation is to use the diameter of the bit. For questions about the Stepdown of the Step over talk to Russ of one of the mentors. When you are finished with these settings select green checkmark .
|
|
A multicolored tool path will be generated on the surface contour of the part.
|
|
Select the Verify button (highlighted) in the Toolpath tab toolbar. A Verify dialog box with playback buttons will appear. Press the play button. The computer will then simulate the part being cut. Toward the bottom of the dialog box you can adjust the cutting speed . A yellow surface indicates a cut. A red surface indicates a collision. If red appears by the end of the simulation, your tool settings need to be adjusted. Select green check mark to exit the Verify dialog box.
|
|
picture of the pop-up playback
|
|
You are now going to do a finishing pass.
Right-click the red arrow > select Mill toolpaths > Surface finish > Parallel.
Re-select the surface contour to be cut. The Surface Finish Parallel dialog box will appear. Select Finish Parallel Parameters tab. Set Max. Step over to at most one half (1/2) the diameter of the tool. NOTE: The smaller the step over the better the surface finish, but the longer the machining time. Select the green check mark.
|
|
Highlight Toolpath Group 1 in the Toolpaths tab on the left side of the screen.
Select the Verify button. Press play to simulate the roughing and finishing passes. If simulation runs correctly, part is finished. Select green check mark .
You are now ready to surface machine your part!
|