Smooth Shaving Device for Arthroscopic Surgeries
$1500 Shave Club Members | |
Sponsors | Dr. William Hiller, MD |
Team Name | $1500 Shave Club |
Duration | Fall 2020 - Spring 2021 |
Faculty Adviser | Dr. Joel Perry |
Team Members |
|
With an interdisciplinary team of engineers working together to solve problems faced by members of the Palouse, we hope to garner technical engineering experience while also creating a product that satisfies our client. The goal from our client is to create a production-ready smooth arthroscopic shaver, capable of robust sterilization and prepared for animal testing. We are working with Dr. Hiller to ensure that our device will be suitable for use in operating rooms around the country by utilizing variable speeds, orbital sanding, and a compact ergonomic design.
Problem Definition[edit | edit source]
Problem Statement
We were tasked with developing a smooth sanding device to be used in arthroscopic surgeries in hopes that it will ease the recovery process for patients. In order to properly sand articular cartilage, variable speed with orbital sanding motion is required to accomplish the desired effect. Our device will also be designed with ergonomics in mind to prevent operating fatigue for surgeons.
Value Proposition
Arthritis is a characteristic roughening of a joint, and causes joint breakdown leading to chronic pain and inflammation. Annually, there are roughly 750,000 knee arthroscopies in the United States, many of which focus on alleviation of arthritic pain in the joint. However, current techniques require cutting out afflicted cartilage or bone, contributing to longer recovery times and increased cost of care. In addition, arthroscopic tooltips are designed for single-use, increasing patient out-of-pocket costs. The goal of this project is to create a device with reusable tooltips that can arthroscopically shave arthritic joint surfaces smooth to lessen pain and lower rehabilitation time. Our device will embody these capabilities via approximation of a random-orbital sanding motion of the shaving platform, as well as offer better ergonomics and user comfort than traditional arthroscopic tools. This tool will enable those suffering arthritic pain to lead comfortable and fulfilling lives.
Background[edit | edit source]
Client Knowledge
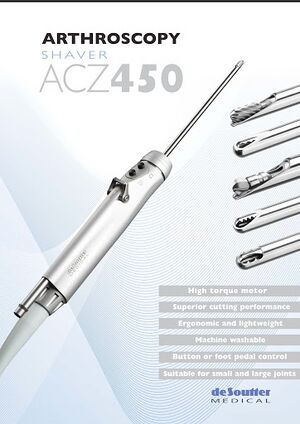
This project was brought to us and sponsored by the incredible, Dr. Doug Hiller. Dr. Hiller is a fellowship trained, sports medicine orthopedic surgeon who participated as the active physician for the Olympic and Paralympic Games. Throughout his years of practice, he found a general consensus amongst experts in the field that there is a gap in the treatment of arthroscopically shaping cartilage in the knee joint. Without the right tool, there is no way to induce cartilage to regenerate without proper stimulation, however no such tool exists. On the other hand, totally replacing the knee could also be appropriate repairable if a device were to be constructed that could smooth the irregular surfaces in the knee. Using instruments designed for other purposes to try to achieve the same results as depicted above typically results in less than ideal outcomes, therefore there is a need for a tool that can work as a smooth arthroscopic shaver.
Current Technology
Current shavers work with solely rotary shaving motions, ripping bits of flesh in a high-speed biting affect. These shavers do not have any sanding mechanism for fine bits of cartilage so the current devices leave ripples or grooves in the tissue. Similarly, the design of current devices has a pencil shaped housing unit opposed to a more ergonomic design.
Active Material

Our device is intended to be used on cartilage, a tissue that decreases friction and distributes loads. Cartilage has a high water content and intensive structural properties which help it shield stress in joints. In cartilage there are 3 layers of collagen fibers running from the superficial, through the middle, to the deep zone. Unlike bone which has faster healing properties, cartilage has a poor capacity for healing which commonly leads to degradation needing surgical intervention.
Previous Project
We are not the first group to be tackling this project, so fortunately we have received a lot of great feedback from the previous group. Although they had a rudimentary prototype, it was inconsistent and not suitable for sustained use. Therefore, we have been asked to take their extensive research and apply it so that a working prototype can be made. In their design, the device operated using an external battery pack and a Sonicare toothbrush motor, however both were recommended for change. The external battery pack prevented the design from being portable and only had a 17 minute run time. The toothbrush motor, although fast, stopped easily due to overloaded force in typical conditions and didn't provide a repeatable manufacturing design. Their design also did not have any speed variability which is crucial for the project. However, the last team did conduct thorough research into sanding grits to find which was the best for articular cartilage. In their tests, they found that 100-400grit sandpaper performed well, with optimal grit being 300. This will be the basis for our design assumptions.
Objective
The objective of this project is to develop a robust smooth sanding device to be used in arthroscopic surgeries to ease patient physical rehabilitation. Building on the thoughts and contributions of the last team, we are tasked with refining the design of an ergonomic shaving device capable of random orbital sanding action and variable toggle speed control. Due to the complexity of arthroscopic procedures, the device must meet industry size constraints for arthroscopy and must be able to withstand corrosion in saline-rich environments. Previously, the last team was responsible for the creation of a first prototype; here, we are instructed to complete prototype refinement according to the shaving and operating parameters they defined during their biological experiments. This device is expected to be used at high performance for an intermittent two hour period, with up to 30 minutes of continuous use without overheating. During and after a surgical procedure, is must be capable of swapping shaving heads, as well as reusable and autoclavable. Finally, the device is requested to be constructed with biologically compatible materials, and cost less than $1500 to prototype.
Deliverables[edit | edit source]
Our deliverable is a working prototype that could be put to production at the end of this course. It must have variable speed, orbital sanding, an ergonomic handle, and be capable of running for extended periods of time at a load. Our objective is to work together as a team to create the said deliverable and give it to the client with the expectation that his money was put to valuable use. Besides that deliverable to our client, each of the team members is responsible for a logbook and the team as a whole is responsible for all of the coursework associated with the Capstone Design Class. This includes a Team Contract, Budget, Project Requirements Document, Project Schedule, Logbook Checks, Portfolio Checks, Wikipage Checks, Snapshots, Deesign Validation Plan, Value Proposition, Concept Design Review, Team Member Citizenships, Design Expo Registration, Engineering Release Review, Technical Presentation, and the Final Expo.
Specifications[edit | edit source]
Product Requirements
After discussions with our client, we have narrowed down the feasible design constraints into the following list:
- Pistol grip style handle
- Variable speed output with 900-6000 RPM oscillation settings
- Random orbital sanding action
- Maximum output shaft diameter of 4mm. Output shaft should be able to withstand corrosion in saline-rich environments
- Compatibility with 100-400 grit shaver heads/burs. 300 grit shaver heads/burs have been previously noted to work the best
- Reliable two-hour battery life
- Compatibility with existing surgical suction pumps. Debris removal during shaving (condyle, menisci cartilage, bone fragments)
- The device should be reusable, and compatible with different shaver heads. Autoclaving (60kPa, 150 degrees Celsius)
- Biologically compatible materials
- Comfortable and lightweight
- Sturdy design suitable for accidental drops
- Less than $1500 to build
Team Roles and Responsibilites[edit | edit source]
In order to effectively tackle such a large project in a relatively short amount of time and bring an idea through prototyping to final development, it was necessary to divide our team into manageable team roles. These roles allowed our team to delve into different components of the various aspects of development. We chose to have Jett Murray be our client correspondent, recorder, circuit designer, and software programmer. Lucas Dibelius was determined to be the component machinist, Wikipage writer and editor, scheduling agent, and purchasing liaison. Maclean Landis was given the role of portfolio compiler and manager, as well as computer aided design (CAD) advisor. Finally, Ryan Crowell accepted the role of financial advisor and budgeting consultant, as well as the CAD lead engineer and 3D printing advisor.
Design[edit | edit source]
Brainstorming and Concepts Considered
When the team first received work from the last group, it was obvious that a new design needed to be created. The device, among other things, did not function when turned on several times. A Sonicare toothbrush was used, which, is known to stall when force is applied to the outside of the shaft. As a shaving mechanism this is a failure mode that could not be tolerated. The team was curious how the random orbital sanding motion requirement could be fulfilled with simple mechanics that would have enough torque to resist bone and cartilage. During the brainstorming phase, many different concepts were pitched by group members.
One that was considered was a linear actuator connected perpendicularly to a DC motor that would push it forward and backward as it spun along a axis that was orthogonal to the axis pushing it. This would create a spiraling motion with the shaver head. This idea was eventually thrown out because the team decided that it would be too difficult to have a DC motor that was not stationary.
Another design we considered was one that was very similar to a Theragun, which is a massaging device that we thought could also be utilized as a sanding motor. These devices were very expensive which prevented us from discovering how they worked internally, not to mention they were fairly large and would be difficult to downsize.
The team also came up with a mechanism that involved a stationary DC motor connected to an output shaft by a slotted connection. The connection would allow for the output shaft to slide linearly while keeping the rotational motion of the DC motor. The output shaft would also be connected to an actuation fork that is between two shaft collars. To create a force on the actuation fork, the team decided to utilize four solenoids parallel with the output shaft. There would be a pair of solenoids below and above the output shaft to minimize the moment created by the solenoids. The front and back solenoid pairs would be turned on separately to push the actuation fork forwards and back. This mechanism would create a motion that combined the traditional drill rotation with a linear actuation that the team believed would leave a smaller groove than current arthroscopic tools.
Another design that the team considered utilized gears to create linear actuation. By using a series of three bevel gears driven by the DC motor, it would be possible to have third gear rotate orthogonally to the first. The third gear also would drive a component that resembles the driveshaft to piston connection of an engine. However, instead of being attached to a piston, the crankshaft is connected to an actuation fork on the output shaft. This design would incorporate the slotted adapter of the previous design to allow for the output shaft to rotate while moving freely in the axis of rotation. One advantage of this design is the ease of coding due to the linear actuation scaling mechanically instead of through the code. The team was unable to create a prototype of this idea because it was not considered until the final prototype was about to be fabricated and did not seem feasible in the time remaining for the project.
During the Concept Design Review presentation, the group was asked if any simulations had been run to prove that the mechanism would create a motion that sands better than current tools. The results of different rotational speeds and linear actuation rates from the simulation run in MATLAB can also be compared in Figure X. The team found that when the rates were scaled to each other the motion created only followed the exact same path throughout time. This can be seen in the two plots on the right side of Figure X. However, if there is a slight change in path when pi was entered into the period of the linear actuation, which, can be observed in the plot on the left. The two plots on the right simulate a motion where the speed of the solenoid actuation scaled with the DC motor. The plot on the left simulates the motion created by solenoid speed being scaled in small incremental steps to a range of speeds of the DC motor.
Material Selection
The outer shaft will be made from 1060 Alloy Aluminum due to its high strength to weight ratio as well as the fact that it is inexpensive and non-toxic. Another unique property that is highly useful to our project is that it is sterilizable, which makes it perfect for handles in surgical equipment. However, due to the high saline environment during use, the aluminum should be coated to reduce corrosion. The inner shaft will be made from 316L medical grade stainless steel because it is still relatively inexpensive, particularly compared to other surgical materials like titanium. Additionally, this allow of steel is commonly used in surgical instruments because it is resistant to corrosion in aqueous and saline environments. This was also chosen because it is strong enough to withstand sandblasting so we could create an integrated gritted sanding head design.
CAD Models
In order to create our device, we went through several iterations of the prototype concept, all of which involving extensive CAD modelling.
The DC motor in conjunction with four solenoids gave us the random orbital motion that was desired. The solenoids were used to actuate the rotating shaft along the same axis that it was spinning about. The shaft used slot such that the shaft could move inward and outward. A key was also utilized so the shaft would continue to rotate with the DC motor as it was pushed around by the solenoids (Figure 6). The reason why four were used was because a solenoid is needed on each side is so that the shaft can be pushed in both directions, the springs to retract the solenoids were too weak to pull the shaft back. The other two solenoids help prevent any unwanted moments on the shaft. Another important feature that was added was a trigger that used an extension spring to give it the same feel as a typical trigger you would feel on a gun. After sizing the spring, the team decided it would be best if the spring was never fully relaxed so that during the full length of the pull the user would feel resistance. A mounting plate that was easily removed was used for the sake of autoclaving (Figure 7). All of the electrical components, as well as the trigger, were attached to it so the user would not have to worry about damaging anything. When the final housing was finished modeling (Figure 8), it was clear that it would not be able to fit as one piece on the Mark Forged 3D printer. To solve this, multiple splits in the CAD model were used, to conjoin these parts embedded nuts and countersunk screws were a necessity to keep the design aesthetic. To allow for fast battery replacement a snap joint door for the battery was created. After the CAD assembly was created, it became obvious that wiring would be an issue especially with a large battery and the addition of a perfboard. The need solution for this problem was to add a second handle in the front to house more of the wires and the perfboard. This second handle also was created thinking ahead towards a device that can utilize a suction pump in the extra space. As far as creating the handle and mounting plate, the team desided to use a carbon fiber inlay which would allow the device to be more robust and durable which would help prevent in the shaft moving off axis.
System Architecture
To achieve design requirements for this device, including an appropriate approximation of random orbital sanding and variable speed output, it was necessary to develop a robust system with a battery that would provide enough longevity for an actual surgery. After working with the client to understand what types of time periods this device would be used for, we aimed to develop the circuity to be active at maximum speed for 30 minutes, followed by two hours of downtime where the device was powered, but not in use. After developing our design criteria, we set to work designing and constructing a circuit that was capable of meeting all requirements.
To simplify microcontroller (5V Adafruit Trinket) programming and enable simple adjustment of operational parameters, we elected to build the rotary component of the device around an existing high-performance motor. To do so, we purchased a commercially available electronic speed controller (ESC) for a radio controlled (RC) airplane, a 1000kV (RPM/volt) motor, and a 100kW potentiometer. Due to the modularity of this setup, we were able to select any compatible 11.1V battery desired; to ensure operational longevity, we elected to purchase a 3-cell 1500mAh lithium polymer (LiPO) battery. The microcontroller was then programmed to interpret the potentiometer’s position via a modified servo library and scale the motor speed appropriately using pulse width modulation from 1 to 2ms. This system theoretically achieved our operational speed requirement of 900-6000 RPM. To achieve linear oscillation and approximate random orbital sanding, we elected to include an actuation fork on the output shaft that was pushed forward and backward by two sets of counter-opposing 12V 5N solenoids. We were able to utilize two MOSFETs that were innervated by the microcontroller to control these solenoids and gate a direct connection to our 11.1V battery. Solenoid speeds were set manually in the code, and adjusted by opening and closing MOSFETs at a variable delay that was scaled through all potentiometer positions. Finally, a master toggle switch and momentary switch were added to the system to activate/deactivate the device and solenoids. Altogether, this setup ensured programmable flexibility for our circuit, as our solenoids and our motor were independently controllable. Thus, we were able to make rapid adjustments to the operating capabilities of the device if indicated. Our final circuit diagram is below.
Project Learning[edit | edit source]
Future Work
Although our team takes immense pride in our final design its functionality, and its ability to reliably meet all design constraints, there can always be room for improvement. Through the design process, we were able to familiarize ourselves with the intimacies of the operational nature for this device; all assumptions that we made about operation were eventually validated in physical testing environments. We were pleased to see that our device performed well and were satisfied with the final product, but experimental testing revealed several areas of improvement that could be modified in the future to better accommodate our client’s specific operational capabilities.
Given the chance to address a few of the potential issues we documented, our first order of business would be to slim down the handle to increase user comfort. Due to initial concerns about feasibility of internalizing all device components, including the internal operating mechanism and the accommodating circuitry, we designed the external housing unit to accommodate excessive storage. However, after completing and assembling the aforementioned internal components within the finished housing unit, we noted that there is an unacceptable amount of awkward, unused space within the device. This space is almost entirely localized to the rear handle/grip area, and widens this area to create a large, uncomfortable grip. Altering our CAD design to utilize this space more efficiently would require an entire redesign of the lower receiver for the device, but If slimmed down the entire handle could be more ergonomic for the user.
Although not immensely oversized compared to the device handle, the upper receiver of this prototype also possesses unused internal space, creating balancing issues for many users. Currently, this area is designed to accommodate four excessively large project-grade solenoids working in tandem; however we believe that these could likely be swapped for parts with less volume, freeing up quite a bit of overhead space inside of the device. Naturally, the concern associated with implementing a change like this one would be assuring that solenoid force output would still be adequate for operation. Trimming out excess space in the upper receiver using smaller solenoids, would result in a device with an overall decreased footprint compared to the current prototype. A complete redesign of the handle implementation of new solenoids would likely cost around $400 dollars, as specific 3D printing materials such as onyx and carbon fiber would be required to retain strength.
To improve operation, extensive testing to determine the perfect combinations of solenoid and rotary speeds could be utilized to improve the sanding results that this device is able to produce. As the electrical system of the device was designed around adjustability, reprograming the microcontroller to include these capabilities would be relatively simple; however, it is likely that several more Matlab simulations and physical tests would need to be completed. For example, we were not able to test the device on cartilage surfaces, as the bovine samples that we acquired from VandalMeats were cross-sections of long bones, and did not contain epiphyses or cartilaginous surfaces. Thus, more modeling and testing will be required to optimize this device, but results of these experiments will be simple and inexpensive to implement.
Final Design[edit | edit source]
Our team went through several iterations of brainstorming before arriving at a final design. Our team began by first analyzing the design from the previous group, dissecting and evaluating the operating mechanism, the circuitry, and the software used; simultaneously judging it against our desired design constraints. The previous team utilized a motor from a Sonicare toothbrush, but the design did not incorporate a random orbital sanding mechanism; thus, we concluded that it was necessary to develop an entirely new design. Initially, we considered the use of several different actuators and motors to achieve both rotational and linear motion. However, we eventually narrowed our focus to three main brainstorming solutions. The first was to have a DC motor mounted perpendicular to the axis of the output shaft, where the motor’s rotational motion would be linearized by a cam shaft to deliver a sanding pattern not unlike the pattern produced by a piston and cylinder operating in an engine. The second was to have a DC motor mounted in line with the axis of rotation of the output shaft that was pushed forward and backward by a linear actuator; this would achieve both linear and rotational action. The third and final thought was to create an internal mechanism in which a slotted adapter was mounted to an inline DC rotational motor, where dual mounted solenoids would move the output shaft back and forth in the slot.
Working Prototype[edit | edit source]
We eventually decided to finalize the third design as our main prototyping solution due to the feasibility of obtaining parts. Due to the restrictions applied by the size constraint of this device, creating a precision piston and cylinder with appropriate tolerances to effectively apply forces translated from a micro-sized camshaft would not have been possible with our resources and machining experience. Similarly, we were unable to find any linear actuators that could be adequately sized to our device, and thus we elected to pursue our third option. After researching and calculating force and speed requirements for both the solenoids and DC motor, the team noted that parts that met our design criteria were readily available; hence, we would be able to prototype and test our design quickly. Pushing this design to testing proved that when we constructed a completed prototype on a test bed, it yielded the exact results we required. As a result, we finalized this design for our project.
Our final design was developed and constructed after our first prototype failed due to frictional force that our 3D printed parts generated at high-speed operation, and incorporates internal aluminum parts that were machinable with the skills and resources that we possessed. From there, the circuit and coding were designed to operate the solenoids and motor in conjunction to create a random orbital sanding motion. To accommodate these components, we created a housing unit large enough to accommodate the output shaft mechanism and circuitry, requiring implementation of unique design solutions to make retain device accessibility. Finally, we were able to incorporate a modular interior and exterior shaft coupler to allow for multiple shaving heads to be swapped onto the device; thus, we met all of our design requirements in the end.
Testing[edit | edit source]
To test the functionality of our final prototype the team created an organized testing regiment to qualitatively determine how well the device could shave down a sharp edge on bone. The team obtained several cow bones from the on-campus meat processing facility to simulate the type of hard organic material that the shaver was designed for. Next, six identical holes were drilled into the side of each bone using an impact driver with a quarter inch drill bit. The team decided that six holes would the best option for testing 3 set rotational and linear actuation speeds for each tooltip. The speeds to be tested were 5000, 7500, and 10,000 rotations per minute with a linear actuation period of 700, 475, and 100 milliseconds respectively. To prove the efficacy of the linear actuation of the tooltip, the team kept the solenoids turned off for each speed and tooltip tested. This acted as a control that was compared against the results obtained from shaving with the linear actuation enabled. To keep the results of testing precise, the team shaved each hole for thirty seconds and applied the same amount of pressure to the device. After each tooltip was tested, the team took high resolution photographs of the bone and qualitatively recorded the resulting smoothness of the edges of each hole.
The results are shown below. The team found that the device had the best results while using the highest grit under a rotational speed of approximately 7500 RPM and a linear actuation period of 475 milliseconds. By comparing the results of using linear actuation and only rotation, there was only one instance where the linear actuation performed worse. This occurred while testing the device on a high speed with the highest grit tooltip. After review of the results, the team has determined that the device functioned as predicted and that combining linear actuation and rotational motion was more effective than rotational motion alone. The device was also capable of maintaining its battery power throughout the two-hour duration of testing, which, was a goal of the device described in the project validation rubric created by the team.
Validation[edit | edit source]
In order to evaluate the effectiveness of our design in comparison to the design constraints and requirements, we created the following table as a way to record our validation results. With this table, one can see our validation plan for our final design, as well as whether it met the standards set forth at the beginning of the design phase. We evaluated our design based on frequency output, battery size, shaft size, shaver head compatibility, battery length, suction pump capability, swappable tips, functionality, final result efficacy, thermostability, reliability under load, and so forth as described in the table. Also listed is the method of testing used to evaluate each parameetr, as well as the test subject, target date, and the results. Finally, the recommendation for each validation standard is listed to help future groups better understand the starting point for them with our finished device.
One of the biggest requirements in this project was to create a device capable of orbital sanding action. Orbital sanding means that there must be at least two routes of motion for the device to function on, and ideally with random action, the device will not wear groves in the same place over and over again. Due to the high operating conditions of the device, this is not possible to evaluate with the human eye nor any resources available to us at the time of testing, so instead a Matlab simulation was created to solve this problem. The Matlab program simulated the pathing of our device and the groove it would wear given its rotational and linear actuated motion, thus allowing us to pick a ratio of operation for them so that they would achieve not only orbital motion, but random as well.
Budget[edit | edit source]
Breakdown
In order to ensure that the project was completed according to the client’s budget constraints, it was necessary for the team to create an approximate budget and record our purchases to ensure accurate financial reflection for the client. This allowed the team to consistently evaluate purchases and adjust the predicted budget to keep the project scope within client needs. The budget can be seen below.
Schedule[edit | edit source]
Breakdown
In order to ensure that the project was completed in a timely manner, it was necessary for the team to compile a schedule at the beginning of the project, adjusting as needed throughout the year. This allowed the team to consistently evaluate our performance and timeline for completion, making any changes to pacing to accommodate the timeframe for finishing the design. The schedule was broken down into course requirements, as well as the actual project development (see below).
Team Members[edit | edit source]
Ryan Crowell
|
Lucas Dibelius
| ||
Maclean Landis
|
Jett Murray
|
Additional Documentation[edit | edit source]
Team Contract
File:1500 Capstone Team Contract.pdf
Product Requirements
File:1500 Product Requirements Document.pdf
Concept Design Review
File:Concept Design Review Sander.pdf
Design Validation
File:1500 Design Validation Plan & Results.pdf
File:Design Validation Plan & Results Template.pdf
Engineering Release Review
File:Engineering Release Review Sander.pdf
Meeting Minutes
File:1500 Team Meeting 1.pdf
File:1500 Team Meeting 2.pdf
File:1500 Team Meeting 3.pdf
File:1500 Team Meeting 4.pdf
File:1500 Team Meeting 5.pdf
File:Team Meeting -6 Agenda, Minutes 10-06.pdf
File:1500 Team Meeting 7.pdf
File:1500 Team Meeting 8.pdf
File:1500 Team Meeting 9.pdf
File:1500 Team Meeting 10.pdf
File:1500 Team Meeting 11.pdf
File:Team Meeting 12.pdf
File:Team Meeting -13 Agenda, Minutes 11-10.pdf
File:Team Meeting -14 Agenda, Minutes 12-1.pdf
File:Team Meeting -15 Agenda, Minutes 12-8.pdf
File:Team Meeting -16 Agenda, Minutes 1-19-21.pdf
File:Team Meeting -17 Agenda, Minutes 1-27-21.pdf
File:Team Meeting -18 Agenda, Minutes 2-2-21.pdf
File:Team Meeting -19 Agenda, Minutes 2-9-21.pdf
File:Team Meeting -20 Agenda, Minutes 2-16-21.pdf
File:Team Meeting -21 Agenda, Minutes 2-23-21.pdf
File:Team Meeting -22 Agenda, Minutes 3-1-21.pdf
Presentations
Snapshot Day #1:
File:1500 Snapshot Day -1.pdf
Snapshot Day #2:
File:Snapshot 2 Sander.pdf
Snapshot Day #3:
File:Snapshot 3 Sander.pdf
Client Interview
File:1500 Client Meeting 1.pdf
Purchased Parts Datasheets
File:Battery Charger.pdf
File:Battery.pdf
File:DC Motor.pdf
File:Microcontroller.pdf
File:Potentiometer.pdf
File:Servo.pdf
File:Solenoid.pdf
File:Speed Controller.pdf
Project Learning
File:Testing Research.pdf
File:Circuit Board Research.pdf
File:Theragun Research.pdf
File:Output Shaft Research.pdf
File:Stainless Steel Abrasive Research.pdf