|
|
|
Team Name
|
Two Stroke Smoke
|
Duration
|
Fall 2017 - Spring 2018
|
Faculty Advisors
|
Dr. Dan Cordon
|
Team
|
- Cade Smith
- Jason Maas
- Phoenix Duncan
|
The goal of this project is to design an exhaust system that will reduce the noise and emissions of a two-stroke snowmobile, without significantly sacrificing power. The system will include a tuned pipe, catalytic converter, muffler, and a controllable backpressure valve. The project will provide a baseline for the next four years of the University of Idaho's Clean Snowmobile Challenge Team.
Problem Definition
Background
Since 2001, students from the University of Idaho have competed in the SAE Clean Snowmobile Challenge. The competition is allows college students to work on reducing the noise and pollutant emissions while increasing the fuel economy of stock snowmobiles. This year, the UI CSC senior design team will be re-designing the entire exhaust system on the snowmobile.
Specifications
Technologies Used
|
Title
|
Image
|
Description
|
Tuned Pipe
|
|
A tuned pipe utilizes pressure waves to reduce the impacts of short-circuited fuels on the two-stroke platform. The tuned pipe is designed to work most effectively over a specified rpm band. Since the engine of the 2018 snowmobile was detuned to meet competition power requirements, the existing tuned pipe needs to be modified.
|
Back-pressure Control Valve
|
|
Two stroke engines are heavily affected by intake and exhaust pressure levels. A valve could be added to the exhaust stream of the snowmobile to increase back-pressure at low engine speeds, increasing engine efficiency and performance.
|
Catalytic Converter
|
|
A three-way catalytic converter is used to reduce harmful emissions by oxidizing CO and unburned hydrocarbons (UHC) and reducing NOx. Because the catalytic converter drastically increases exhaust stream temperatures, it should be placed at the exit of the muffler to improve muffler life.
|
Muffler
|
|
The 2016 UICSC senior design team designed and manufactured a muffler that reduced the noise produced by the snowmobile, but was not durable enough to withstand the exhaust temperatures and produced too much backpressure. This year's design should follow the example of last year's, while increasing durability and reducing backpressure.
|
Deliverables
- An exhaust system that can be used by the UICSC team for the next four years
- Sound level and flow simulations for the muffler.
- A GT Power model for the engine and tuned pipe
- Heat transfer and flow simulations for the catalyst and muffler
- Documentation of control system and manufacturing plans
Design Components
Tuned Pipe
Image |
Description
|
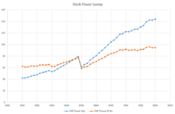 |
Since the tuned pipe operates most efficiently over a specific band of engine speeds, we need to modify ours to match our reduced-speed engine. The first step in this process was to run a power sweep on the dynamometer to determine what the engine's peak rpm would be. A stock 850 E-TEC power sweep recorded by the Two-Stroke Smoke team is shown to the left.
|
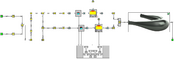 |
The next step was to create a model in GT Suite that would optimize tuned pipe length for a given engine operating range. To do this we had to measure and create math models to describe the exhaust ports, intake ports, RAVE valves, and air intake. The math models were created in Matlab.
|
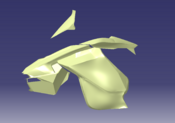 |
Once we knew the optimal length of the tuned pipe, we needed to weld extension pieces into the header and dwell sections of the tuned pipe to reach that length. We used a laser scanner to create an open volume that matches the inside of the snowmobile in SolidWorks, then modeled a few tuned pipes of the correct length until we found one that would fit in our chassis.
|
 |
We then modified the tuned pipe and tested it against the stock tuned pipe on the dynamometer. As can be seen in the plot on the left, we saw an increase in torque across the new operating range and peak torque increase of 5 ft-lb at 6800 rpm.
|
Muffler
Image |
Description
|
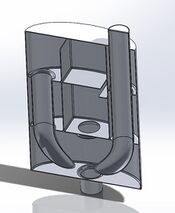 |
Since a muffler was created last year by the UICSC team that passed the sound event at competition, we decided to follow their core design. We made numerous small design changes to reduce back-pressure in order to accommodate the exhaust baffle. We also needed to make our muffler more durable, so we talked with sponsors and obtained sound materials that would stand up to higher temperatures.
|
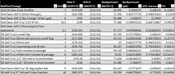 |
Every design change from the 2016 muffler was simulated using SolidWorks Flow Simulation. The chart to the left (click to expand) shows the simulated back-pressure difference that each modification made. Overall, flow simulations predicted a 50% decrease in backpressure using the final design, but flow bench testing showed a 2% decrease.
|
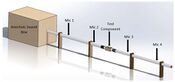 |
To verify that our muffler would be as quiet at the 2017 muffler, we tested it on an anechoic sound box. The anechoic sound box produces pure frequencies from 80 to 2000 Hz, and measures the transmission loss through the test piece.
|
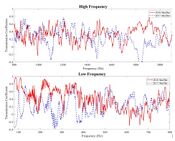 |
The plot on the left shows the results from sound box testing. Overall, the 2017 muffler had a transmission coefficient of 0.4, compared to the 2016 muffler's 0.2. This means that over the 2000 Hz range, the 2017 muffler will reduce more noise. The 2017 muffler significantly outperforms the 2016 muffler in the 0-400 and 1700-2000 Hz ranges.
|
Exhaust Baffle
Image |
Description
|
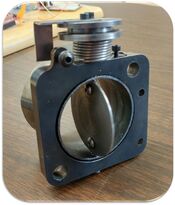 |
The exhaust baffle was researched and based off exhaust throttles tested on performance motorcycles in the late 1980's. It was designed and manufactured in house, to be used in exploratory testing on the dynamometer.
|
Catalytic Converter
Image |
Description
|
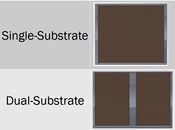 |
Two types of catalytic converters were tested for use on the 2017 UICSC entry. One contains a single substrate the continues for the length of the catalyst, while the other contains two substrates separated by a 10 mm gap. This gap acts as a tripped boundary, inducing turbulent flow through the second substrate, which means better mixing and more emissions reduction.
|
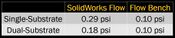 |
Both styles of catalytic converter were simulated using Solidworks Flow Simulation and using the flow bench. We believe that the Solidworks simulations under-estimate the backpressure of the dual-substrate catalyst compared to the single-substrate because the tripped boundary effect was not represented.
|
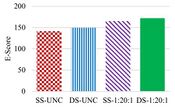 |
The emissions characteristics of 5 catalysts were tested using the CSC's E-score test. Coated and uncoated configurations of both a dual substrate and single substrate catalyst were tested, along with a stock system with no catalyst. The E-score is a function of emissions output at 5 operating conditions seen most often when riding. A score of 175 is required to pass National Park Service emissions requirements, while a perfect score of 210 means the snowmobile is producing only CO2, H20, and N2. With a dual-substrate catalytic converter the UICSC snowmobile produced and E-Score of 178.
|
Team Information
Picture |
Bio |
Discipline
|
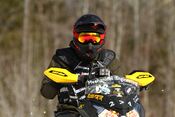 |
Cade Smith: Cade is a senior studying mechanical engineering. His focuses are in engine development, combustion, and manufacturing. His hobbies include camping, hiking, and playing guitar.
|
Mechanical Engineering
|
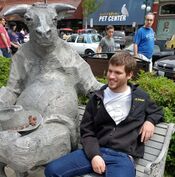 |
Jason Maas: Jason is a senior studying mechanical engineering. His focuses are in numerical methods, robotics, and FEA. His hobbies include camping, hiking, and playing guitar.
|
Mechanical Engineering
|
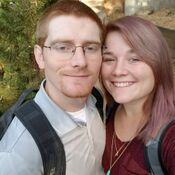 |
Phoenix Duncan: Phoenix is a senior studying mechanical engineering. His focuses are in robotics, FEA, and sustainable energy. His hobbies include vehicle repair/restoration and spending time with his fiancee and their dogs.
|
Mechanical Engineering
|
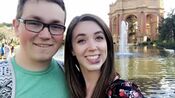 |
Zachary Lipple: Zachary was a senior in mechanical engineering and is spending the spring semester working a co-op for Borg Warner. His focuses are in small engine and vehicle development.
|
Mechanical Engineering
|
Document Archive
Other Documents
Return to Contents